Phenolic Resin for Brake Pads – Utilizing Unique Chemistry Technology for Braking
Reduces Noise, Vibration and Other Unpleasant Properties when Braking!
- Do you have the following problems?
- ・Noise is emitted when brakes are applied.
- ・Brakes make noise when they are applied in the morning.
- ・Unpleasant vibration felt on brake pedal and steering wheel when braking.
- ・Would like brakes that don’t leave black residue on wheels.
- ・Enjoy driving on mountain roads and would like to drive on a race course!
What is Milex™?
Milex is a special phenolic resin that features moldability, superior thermal stability, low moisture absorption and high chemical resistance.
As a phenolic resin that has a long history, Milex constantly responds to the latest needs and is utilized to take on the challenge of developing cutting-edge technologies.
The XL-series features superior thermal resistance and low moisture absorption.
The RN, RS and RM-series of elastomer modified phenolic resin are provided with the advantages of both elastomer and phenolic resin, and feature superior impact resistance.
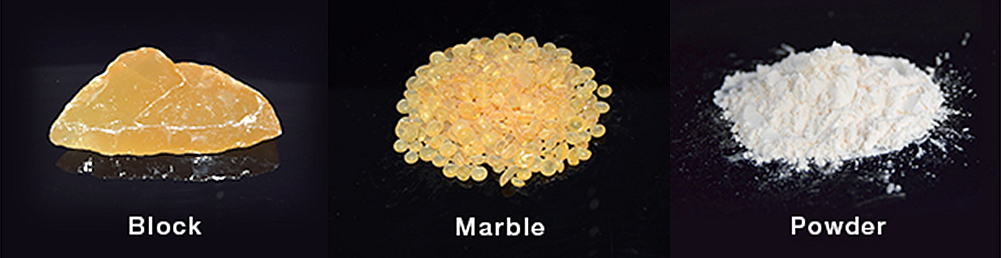
Milex™ at work around the globe
Milex has been involved in the evolution of brake pads for over a quarter century.
This technology which was created in Japan has played a large role in solving the problems of squeaking noise and vibration for brakes.
In addition to Japan, it is being extensively utilized in Korea, China, Thailand and Taiwan in Asia, as well as in North America and Europe.
We would like to continue to help vehicles around the world to stop safely, while making them more comfortable and environmentally friendly.
We hope that you will try out Milex special phenolic resin products.
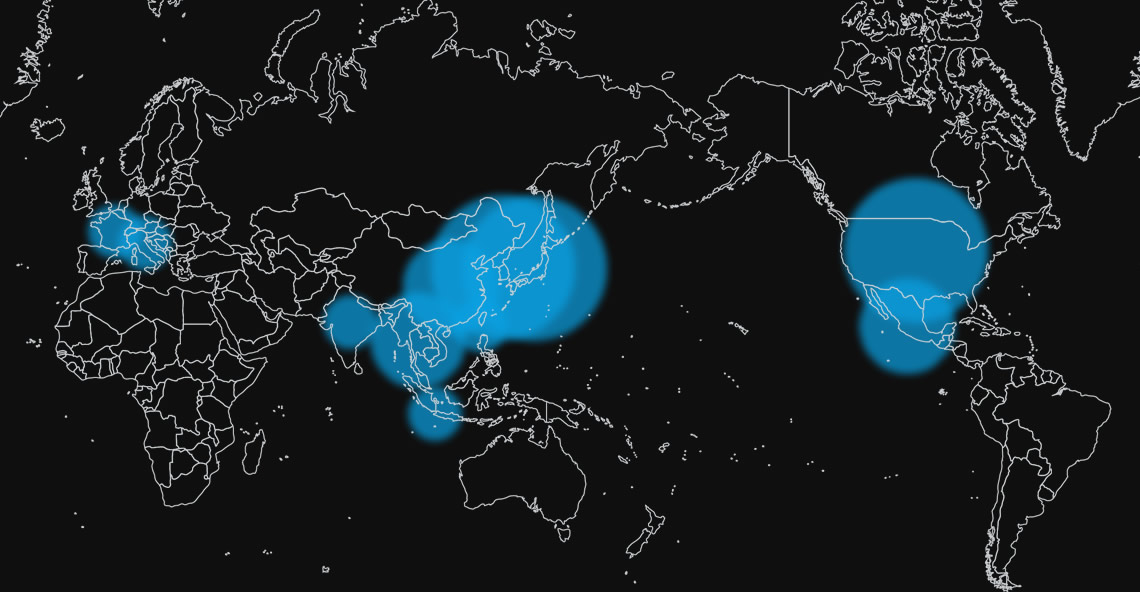
Milex has been utilized in a wide range of fields, mainly as a binder for brake pads
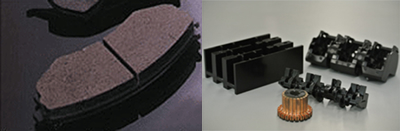
[Main Applications]
Binder for friction materials
Binder for molding materials (compounds)
Binder for grinding wheels
Heat-resistant adhesive
Binder for heat-resistant/powder coatings
Various series respond to wide variety of demands
RN/RS-Series
This is a novolac type of phenolic resin. The RN-series is a special acrylic rubber modified resin and the RS-series is a silicone rubber modified resin. Both of these series feature superior moldability, heat resistance, impact resistance and chemical resistance.
RN-Series Acrylic rubber modified resin
・Flexibility
・Crack resistance
・Chemical resistance
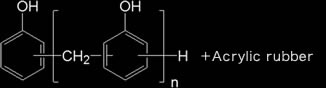
RS-Series Silicone rubber modified resin
・Flexibility
・Water resistance
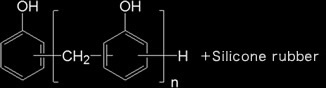
XL-Series
This series utilizes a Phenol-Aralkyl resin that features high heat resistance, wear resistance and chemical resistance, and exhibits superior vibration properties.
XL-Series Phenol-Aralkyl resin
・Flexibility
・Water resistance
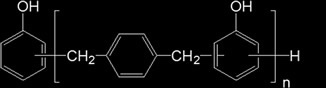
RX-Series
This resin combines thermal stability and moldability in an optimum balance.
RM-Series
Special polyolefin is dispersed in order to provide vibration absorption and wear resistance.
RM-Series Special polymer modified resin
・Flexibility
・Wear resistance
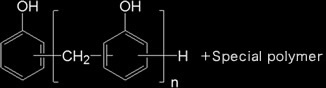
Verification of Milex™ features
Milex™ RN-Series focuses on improving NVH with high vibration absorption
The Milex RN-Series exhibits particularly superior vibration absorption by uniformly dispersing special acrylic rubber inside the resin. Vibration absorption bands in various temperature ranges can be selected according to the type of rubber and the amount of modification.
Product | Softening Point (℃) |
Flow/125℃ (mm) |
Gel Time (s) |
Amount of Modification (phr) |
---|---|---|---|---|
RN-2410MB | 93~102 | 25~45 | 80~130 | 10 |
RN-2330MB | 90~108 | 12~27 | 80~140 | 30 |
RN-2830MB | 93~103 | 20~32 | 92~148 | 30 |
RN-2830MR | 88~100 | 18~32 | 40~100 | 30 |
- Product
- RN-2410MB
- Softening Point(℃)
- 93~102
- Flow/125℃(mm)
- 25~45
- Gel Time(s)
- 80~130
- Amount of Modification(phr)
- 10
- Product
- RN-2330MB
- Softening Point(℃)
- 90~108
- Flow/125℃(mm)
- 12~27
- Gel Time(s)
- 80~140
- Amount of Modification(phr)
- 30
- Product
- RN-2830MB
- Softening Point(℃)
- 93~103
- Flow/125℃(mm)
- 20~32
- Gel Time(s)
- 92~148
- Amount of Modification(phr)
- 30
- Product
- RN-2830MR
- Softening Point(℃)
- 88~100
- Flow/125℃(mm)
- 18~32
- Gel Time(s)
- 40~100
- Amount of Modification(phr)
- 30
Moldability is provided by adding acrylic rubber, which also improves NVH since this boosts vibration absorption.
Upper graphic: Dynamic viscoelasticity, Lower graphic: Vibration absorption
Milex™ RS-Series features water resistance, heat resistance and vibration absorption
The Milex RS-series is a product that provides the optimum balance of water resistance, heat resistance and vibration absorption by uniformly dispersing silicone rubber inside the resin with unique technology.
Product | Softening Point (℃) |
Flow/125℃ (mm) |
Gel Time (s) |
Amount of Modification (phr) |
---|---|---|---|---|
RS-2210MB | 93~103 | 30~46 | 74~130 | 10 |
RS-2230MB | 107~115 | 10~42 | 60~160 | 30 |
- Product
- RS-2210MB
- Softening Point(℃)
- 93~103
- Flow/125℃(mm)
- 30~46
- Gel Time(s)
- 74~130
- Amount of Modification(phr)
- 10
- Product
- RS-2230MB
- Softening Point(℃)
- 107~115
- Flow/125℃(mm)
- 18~26
- Gel Time(s)
- 83~105
- Amount of Modification(phr)
- 30
An improvement in NVH can be expected since heat resistance is the same or higher than straight novolac, and this series has superior moldability.
Upper graphic: 300℃ heat resistance, Lower graphic: Dynamic viscoelasticity
Uniform dispersion of silicone rubber inside the resin eliminates lowering of the elastic modulus when the temperature rises, and provides stable braking performance in all temperature ranges.
Milex™ XL-Series provides substantially higher heat resistance and moldability than straight type
The Milex XL-series is a product that provides a large increase in heat resistance and vibration absorption by introducing the benzyl group into the molecular structure.
Product | Softening Point (℃) |
Flow/125℃ (mm) |
Gel Time (s) |
Remarks |
---|---|---|---|---|
XL-225MB | 88~96 | 38~60 | 150~290 | |
XL-325M | 90~100 | 15~45 | 120~140 | High molecular mass type |
- Product
- XL-225MB
- Softening Point(℃)
- 88~96
- Flow/125℃(mm)
- 38~60
- Gel Time(s)
- 150~290
- Product
- XL-325M
- Softening Point(℃)
- 90~100
- Flow/125℃(mm)
- 15~45
- Gel Time(s)
- 120~140
- Remarks
- High molecular mass type
This product features moldability and substantially increases heat resistance compared to straight type by introducing the benzyl group into the molecular structure.
Upper graphic: 300℃ heat resistance, Lower graphic: Dynamic viscoelasticity
Milex™ RM-Series dramatically enhances wear resistance
This product features moldability and substantially increases heat resistance compared to straight type by introducing the benzyl group into the molecular structure.
Product | Softening Point (℃) |
Flow/125℃ (mm) |
Gel Time (s) |
Remarks |
---|---|---|---|---|
RM-8022MB | 108~118 | 21~28 | 94~137 | |
RM-8322MB | 108~113 | 23~29 | 103~118 |
- Product
- RM-8022MB
- Softening Point(℃)
- 108~118
- Flow/125℃(mm)
- 21~28
- Gel Time(s)
- 94~137
- Product
- RM-8322MB
- Softening Point(℃)
- 108~113
- Flow/125℃(mm)
- 23~29
- Gel Time(s)
- 103~118
This product increases wear resistance by blending special polyolefin that has higher interface strength with phenolic resin, and RM-8322MB features vibration absorption through the moldability of a special polymer.
Upper graphic: Dynamic viscoelasticity, Lower graphic: Wear resistance
Glossary
A
C
D
F
H
J
L
N
P
S
W
Term | Explanation |
---|---|
AK Master | One measurement method in Europe using dynamometer. |
Asbestos material | Asbestos was widely used before as a reinforcement material for friction materials because of its high heat resistance, but usage in Japan has been prohibited since the 1990s after it was determined that it is harmful to health. |
Term | Explanation |
---|---|
Coefficient of friction | Ratio of frictional force acting parallel to contact surface of two objects and normal force (pressure) acting perpendicular to that surface. F = μN |
Compressive strain | Amount of decrease in the thickness of pads and linings with respect to initial thickness due to compression force and temperature. The thickness is measured in the direction in which force is vertically applied to the friction surface. |
Copper free | Regulations on use of copper in friction materials introduced in California (USA) with the objective of reducing environmental load. These regulations prohibit the sales of friction materials containing 5% or more copper from 2021 as well as incorporation in new vehicles, with this value being reduced to 0.5% or more from 2025. |
Term | Explanation |
---|---|
Dust | Wear particles generated due to pad and rotor friction. |
Term | Explanation |
---|---|
Fade | Phenomenon of significant decrease in friction coefficient due to increase in temperature of working surface of pads and rotors as a result of continuous usage of brakes. |
Fade recovery | Evaluation of the extent to which coefficient of friction has recovered before and after fade. |
Term | Explanation |
---|---|
Hardness | Rockwell hardness. Value obtained using the following formula from the difference in penetration depth h (mm) of indenter before and after (twice) when a preliminary test force is first applied using an indenter and the preliminary test force is applied again. Rockwell hardness (HR) = 130 – 500h |
Term | Explanation |
---|---|
JASO | (J) Japanese (A) Automobile (S) Standards (O) Organization. Standard established by JSAE (Society of Automotive Engineers of Japan) that determines technical specifications etc. for automobiles and related parts. |
Judder | Abnormal vibration occurring when brakes are operated. |
Term | Explanation |
---|---|
Low steel material | Friction material that contains 10 – 30% steel fibers. Performance and heat resistance is higher compared to NAO material. |
Term | Explanation |
---|---|
NAO | N (Non), A (Asbestos), O (Organic). Contains less than 10% steel fibers. |
Noise | Abnormal noise generated when brakes are applied. Other names such as squeal, groan and moan are used depending on the frequency of the sound. |
NVH | N(Noise),V(Vibration),H(Harshness) |
Term | Explanation |
---|---|
Porosity | Free volume (void ratio) included in pads or linings. |
Term | Explanation |
---|---|
Scoring | Parallel record shaped striations generated in sliding direction on friction surface of rotors or drums. |
Semi-metallic material | Friction material that contains 30% or more steel fibers. Features superior braking force, fade resistance and wear resistance at high temperatures. |
Speed spread | Phenomenon of friction coefficient of friction material dramatically decreasing with increase in speed of automobile. |
Squeal | High frequency noise generated by resonance between brake system members. |
Term | Explanation |
---|---|
Water recovery | The coefficient of friction decreases when friction material gets wet. Water recovery is the behavior of the coefficient of friction recovering due to the removal of water during braking. |
Wear | Wear, wear damage due to frictional heat. |
Wheel soiling | Soiling of wheels by dust generated by wearing of friction materials. |